Diseño del transportador de banda para la gravilla, de la cantera Lagunillas, Cuba
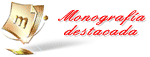
- Introducción
- Materiales y métodos
- Conclusiones
- Recomendaciones
- Bibliografía y referencias bibliográficas
- Anexos
RESUMEN
El presente trabajo de diploma está enfocado en la necesidad de desarrollar una metodología de diseño de un trasportador de banda dada la necesidad de la construcción de una cantera de áridos para la construcción. En este se reflejan los pasos que fueron necesarios para realizar dicho diseño, el cual facilita la información técnica necesaria para construir el transportador de banda para la gravilla, que forma parte de la producción en la Cantera de Lagunillas del municipio San Juan y Martínez.
Para cumplir el objetivo de esta tarea se determinaron los parámetros necesarios a utilizar en el mismo, dado así como la selección del moto-reductor. Incluyendo una valoración económica, se demuestra que resulta factible el trabajo realizado, ya que es más costoso adquirir el transportador en el mercado internacional. Se tiene en cuenta el impacto medioambiental. Así como se establece un régimen de mantenimiento de dicho transportador.
Palabras Calves:
Moto-reductor, transportador de banda
SUMMARY
This diploma work is focused on the need to develop a methodology for designing a conveyor band given the need to build a gravel quarry for construction. This reflects the steps that were necessary to complete this design, which provides the technical information needed to build the conveyor belt for gravel, part of the production in the quarry Lagunillas municipality San Juan y Martinez. To meet the objective of this task required parameters were determined using the same, as well as the selection of the gear motor. Including an economic assessment, we show that it is feasible to work, as it is more expensive to acquire the carrier on the international market. It takes into account the environmental impact. Just as a maintenance regimen of said carrier is established.
Key Word:
Gear motor, belt conveyor.
Introducción
Los transportadores son muy comunes y de vital importancia en procesos de producción, ya que estos disminuyen el esfuerzo de trabajo y eleva la eficiencia del proceso de producción. Estos dispositivos de transporte poseen una amplia gama de aplicaciones. Los transportadores de bandas forman parte de esta familia, los cuales a través del moto-reductor el cual producen el impulso del movimiento a una velocidad ajustada, esto contribuye a un correcto funcionamiento de la misma.
La empresa de Materiales de Construcción y Montaje Industrial de la provincia de Pinar del Río necesita diseñar un transportador de banda para el traslado de la gravilla desde la zaranda hasta la torva, el cual se pondrá en funcionamiento en la cantera de Lagunilla, pero no dispone de la información técnica requerida para lo mismo.
Se propondrá y analizará todos los elementos y componentes que posee dicho trasportador así como su mantenimiento. Se llevara a cabo un análisis económico y el impacto medio ambiental.
Diseño de Investigación
Problema: La carencia de un transportador de banda, contribuye de forma negativa en la productividad de la cantera Lagunilla, por lo que se requiere desarrollar una propuesta de diseño para la fabricación del transportador de banda.
Objeto: Diseño del Transportador de banda.
Campo de acción: Las metodologías de diseño del transportador de banda.
Objetivo: Realizar el diseño del transportador de banda, con el fin de utilizarlo en la producción de la cantera Lagunilla.
Hipótesis: El análisis de los materiales a utilizar, dimensiones, resistencia de sus elementos componentes y sus condiciones de explotación, permitirán el diseño del transportador de banda y su posterior explotación en la cantera Lagunillas.
Tareas a ejecutar:
1- Búsqueda bibliográfica relacionada con el tema.
2- Metodología de cálculo del transportador de banda.
3- Selección del moto-reductor de velocidad.
4- Metodología de cálculo de la transmisión por cadena.
5- Diseño de los árboles.
6- Política del mantenimiento.
7- Valoración medio ambiental.
8- Valoración económica.
CAPÍTULO 1: REVISIÓN BIBLIOGRÁFICA
1.1. El principio de funcionamiento del transportador de banda.
Los transportadores de banda son comúnmente utilizados para transportar objetos que tienen una superficie de fondo irregular, pequeños objetos que puedan caerse de entre rodillos o bolsas con producto que pueda atorarse entre los rodillos. Los transportadores de banda son construidos generalmente de la misma forma: con un marco metálico y con rodillos en los extremos de cada transportador sobre una cama metálica. En aplicaciones donde el producto es demasiado pesado, la cama metálica es sustituida por rodillos. Los rodillos permiten que los objetos sean transportados reduciendo la fricción generada sobre la banda. Los transportadores de banda pueden ser fabricados con secciones curvas. Estos sistemas de transportadores de banda son comúnmente utilizados en oficinas postales o en los aeropuertos para manejo del equipaje de pasajero.
Un transportador de banda (fig. 1) consta en general de dos tamboras, una de ellas motriz (1) y la otra de cola (2), unidas entre sí por una banda (3), la cual se mantiene en tensión por un sistema de atensado (4). Para evitar que se produzca una flecha grande en la banda, esta se apoya sobre rodillos de apoyo (5), en la rama cargada (6) y en la descargada, los están sujetos a la estructura (7) del transportador. El movimiento de la banda es impartido a través de la tambora motriz, por el sistema de la transmisión (8). La figura 2 muestra el esquema del moto-reductor.
La carga se coloca sobre la banda mediante una tolva alimentadora (9) que suministra constantemente material al transportador. La descarga se efectúa a través de un canal (10) que dirige el material a la salida del transportador. Existen dispositivos que permiten la descarga intermedia.
El transportador puede tener también tamboras deflectoras (11), para cambiar el sentido del órgano de tracción por necesidades constructivas, y limpiadores que pueden ser externos e internos.
En algunos casos (fig. 2) la banda en vez de estar apoyada sobre rodillos está apoyada sobre una guía fija (14), solución que se usa preferentemente para la transportación de bultos. (Oriol Guerra, J. M. (1993). Conferencias de Máquinas Transportadoras. La Habana. Félix Valera)
Figura 1. Esquema del transportador de banda.
Figura 1.a. Esquema del moto-reductor.
Figura 2. Esquema de los tipos de apoyos de la banda
1.2. Características de los transportadores de bandas.
Variedad en la manipulación de materiales: El transportador de banda es efectivo en la transportación de una gran variedad de materiales a granel, los cuales pueden ser livianos o pesados, secos o húmedos, polvorientos o en grandes terrones. Se pueden transportar también materiales corrosivos y abrasivos, muchos tipos de bultos y hasta objetos cuya manipulación es delicada, ya que la transportación se efectúa de una forma uniforme y suave.
Rango amplio de capacidades: Debido a los diferentes anchos de banda, la diversidad de materiales que se pueden transportador y la variedad de velocidades en que se opera el transportador de banda, hace que el rango de capacidades sea desde alguno hasta miles de kilo newton por hora.
Rango amplio de longitudes de transportación: El transportador de banda es efectivo tanto para longitudes de pocos metros como para grandes distancia y un solo transportador puede llegar a cubrir 4 ó 5 Km. Si los transportadores de banda se colocan en serie, las distancias a cubrir serian ilimitadas. Actualmente existen instalaciones con transportadores de banda que cubren distancias mayores de 15 km, un ejemplo es el transportador que lleva el mineral de las minas de Pinares de Mayarí a la planta procesadora.
Posibilidad de descarga de material en varios puntos: Un transportador de banda puede realizar la descarga del material al final de su trayectoria pero también, con la utilización de carros de desvío y cuchillas desviadoras se logra realizar descargas intermedias.
Estructura liviana: Debido a las velocidades en que se opera el transportador de banda, el peso lineal de la carga es bajo en comparación con la capacidad manipulada, lo que permita que la estructura sea simple y liviana.
Trazas horizontales e inclinadas: Por el principio de funcionamiento, la traza en un transportador de banda se encuentra siempre en el plano vertical.
Desgaste mínimo y fácil mantenimiento: Debido a que no existe movimiento relativo entre el material y la banda y, además, el material no está en contacto con el resto de las partes móviles del transportador, el desgaste es mínimo. El mantenimiento de la instalación normalmente consiste en una lubricación periódica, a las partes móviles del transportador, incluyendo el sistema propulsor.
Poco consumo de energía: El transportador de banda es el que consume menos potencia por tonelada de material manipulado, principalmente por la característica mencionada en el punto anterior.
A las características explicadas se puede añadir que el funcionamiento de los transportadores de banda es muy uniforme y silencioso y, además, su construcción y montaje es simple comparado con otros transportadores. (Oriol Guerra, J. M. (1993). Conferencias de Máquinas Transportadoras. La Habana. Félix Valera)
1.3. Aplicación de los equipos de transporte industrial.
En los últimos años, los equipos transportadores se han desarrollado considerablemente y se han destacado por ser un medio de transporte muy económico.
En casi todas las industrias, los equipos transportadores sirven para una gran variedad de propósitos, además tienen una amplia utilización en otras aplicaciones comerciales y de servicios. Estos equipos permiten el transporte con un flujo uniforme de una operación a otra, además, efectúa muchas otras funciones tales como distribuir el material, carga a granel y llenado de contenedores.
Su función principal es garantizar la continuidad de las operaciones teniendo en cuenta sus características, aplicaciones y tipo.
(http://www.QuimiNet.com/ transportadores industriales.html)
Máquinas de Transporte Continuo:
Instalaciones Neumáticas.
Instalaciones Hidráulicas.
Transportadores.
Transportadores:
1. Con órgano de tracción Flexible:
Banda.
Tablillas.
Rastrillo.
Cangilones.
Bandejas.
Aéreo.
Elevadores de Cangilones.
Elevadores de Bandejas.
2. No Flexibles:
Sin Fin.
Rodillos.
Vibrantes.
Oscilantes.
1.4. Aplicación.
Los transportadores son utilizados como componentes en la distribución automatizada y almacenamiento. En combinación con manejo equipos computarizados que permiten que se realice eficientemente el almacenamiento, manufactura y distribución de materiales en la industria. Es considerado además como un sistema que minimiza el trabajo que permite que grandes volúmenes sean movidos rápidamente a través de procesos, permitiendo a las empresas embarcar o recibir volúmenes más altos con espacios de almacenamiento menores con un menor gasto.
1.5. Ventajas del transportador de banda.
El transportador de banda es el transportador más difundido dentro de las máquinas de transporte continuo para la transportación de materiales a granel y por piezas en la industria, en la construcción, agricultura y otros.
El elemento principal de un transportador de banda es la banda sinfín flexible. Según los rodillos a utilizar la banda puede tener forma plana o acanalada. El ramal superior cargado y el inferior vacío son suspendidos por medio de rodillos. El movimiento le es suministrado por medio del tambor motriz el cual es puesto en movimiento por medio del motor y reductor. El tensado constante de la banda se garantiza por el dispositivo de tensado. La carga es depositada en la banda por medio del dispositivo de carga y se descarga por el tambor motriz o en el intermedio por medio de dispositivos especiales.
La productividad de un transportador de banda con velocidad de 5 – 8 m/s y ancho de 2400 – 3000mm puede alcanzar hasta 20000 – 25000 T/h. La longitud de transportadores de banda horizontales con bandas de alta resistencia alcanza de 5 – 10 km.
1.6. Materiales a Utilizar.
Estructura soporte metálica (Aceros estructurales).
La cinta o banda, normalmente de goma.
Aceros para los árboles de las tambora: Aceros cementables.
Aceros para los cojinetes de rodamientos: Acero cromado, acero al cromo níquel.
1.7. Lubricantes y Mantenimiento.
* Se utilizan lubricantes líquidos y semisólidos.
– Limpieza de todas las partes componentes del equipo.
– Inspección y revisión de todos los elementos de la máquina.
– Ajuste del mecanismo.
– Nos apoyaremos para dar una clasificación del mantenimiento en los grupos selectivos directivo y generales.
1.8. Partes componentes de los transportadores de banda.
Rodillos de apoyo: La función principal es sostener la banda, para que la flecha de esta no sea mayor de lo permisible. Uso, para la manipulación de gráneles.
Los rodillos se clasifican en:
– Según su aplicación (ubicación en la traza):
Superiores (soportan la rama cargada) (planos y acanalados).
Inferiores (soportan las descargadas) (plano).
*Los rodillos superiores planos se emplean en la transportación de cargas en bulto y para materiales a granel que tengan un ángulo de reposo superior a 30º y que la capacidad transportada no sobrepase los 25 m³/h o cuando la descarga es por medio de una cuchilla desviadora. Estos pueden estar compuestos de uno a cinco rodillos, si es por uno son planos y si es por varios son rodillos superiores acanalados. Los apoyos de dos rodillos se usan para anchos de banda de 300 y 400 mm en transportadores móviles. Los de tres rodillos son los más utilizados, los de cinco se emplean para B (1400 mm).
*Los rodillos inferiores tienen un solo rodillo y siempre son planos.
Según su función:
Normales (apoyo).
Especiales (amortiguantes, limpiadores y centrantes).
Los amortiguantes se colocan en la zona de carga, con el objetivo de amortiguar la caída del material sobre la banda. Son pocos usados.
Los limpiadores se colocan en la rama descargada, con el objetivo de desprender las partículas del material que se adhiere a la banda.
Los rodillos centradores se colocan en la rama cargada y descargada, se usan en trazas mayores de 40 m y la separación entre los rodillos centradores es de 20 – 25 m. Su función es evitar que la banda salga de los rodillos de apoyo.
Según su construcción:
Rígidos {ejes pasantes (más usados), semiejes}.
Suspensión {ejes flexibles}.
El parámetro fundamental de los rodillos de apoyo es el diámetro, para la selección del mismo se debe tener presente, que el momento de fricción creado al estar en contacto la banda sin carga con el rodillo sea mayor que el momento de fricción en los cojinetes pues de lo contrario la banda se deslizaría sobre el rodillo.
1.9. Reductor de velocidad.
Toda máquina cuyo movimiento sea generado por un motor (ya sea eléctrico, de explosión u otro) necesita que la velocidad de dicho motor se adapte a la velocidad necesaria para el buen funcionamiento de la máquina. Además de esta adaptación de velocidad, se deben contemplar otros factores como la potencia mecánica a transmitir, la potencia térmica, rendimientos mecánicos (estáticos y dinámicos).
Esta adaptación se realiza generalmente con uno o varios pares de engranajes que adaptan la velocidad y potencia mecánica montados en un cuerpo compacto denominado reductor de velocidad.
Usos de los reductores de velocidad:
Los reductores de velocidad se los utiliza para todo tipo de máquinas, aunque sean grandes o pequeñas, las máquinas son el corazón de una industria y para ello se necesita que estas funcionen a la velocidad requerida. Sin los reductores de velocidad o moto reductores las máquinas pueden fallar en su funcionamiento. El gran desarrollo que han tenido los moto-reductores ha ocasionado que las fábricas los utilicen más a menudo, debido a que son más simples y compactos.
Los moto-reductores ocasionan diferentes tipos de beneficios como una regularidad perfecta de la velocidad, como también la potencia, mayor eficiencia en la transmisión, mayor seguridad en la transmisión, mayor rigidez en el montaje y menor tiempo necesario para la instalación.
Gracias a la invención de estos reguladores de velocidad la industria ha crecido mucho y ha logrado mejor calidad y eficacia.
(http://es.overblog.com/Como_funcionan_los_reductores_de_velocidad_usos_y_tipos_de_reductores-1228321783-art164436.html)
1.10. Metodología a seguir para el diseño del transportador de banda.
El cálculo de los transportadores se realiza de la siguiente forma:
Lo primero que hay que determinar en el diseño de un transportador son los parámetros geométricos y tecnológicos, como: La traza y los tramos las inclinaciones, determinando la inclinación máxima, los puntos de entrega y alimentación del transportador, las condiciones de operación (humedad, temperatura, agresividad del ambiente).
A continuación se determinan las características de los materiales.
Acto seguido se determinan los parámetros fundamentales, es decir, el ángulo admisible de inclinación del transportador, velocidad y el ancho de la banda, espesor de revestimiento, fuerza de tracción, potencia de la transmisión, tensión de la banda, su número de capas, los diámetros de los tambores y rodillos, paso de los rodillos de apoyo, se seleccionan motores eléctricos, reductores. Para obtener estos parámetros debe seguirse una secuencia lógica.
Figura 3.Transportador de banda.
1.11. Metodología a seguir para el cálculo de la transmisión por cadena.
Debido a no contar con el reductor que garantice los parámetros necesarios en el problema planteado, se hace necesario diseñar una transmisión que nos garantice. En las condiciones de trabajo imperantes de atmósfera polvorienta es preferible una transmisión por correas trapezoidales, pero al contar con un moto-reductor y no un reductor me obliga a ubicar la transmisión a la salida del moto-reductor donde es preferible la transmisión por cadena. Para el diseño de una transmisión por cadenas primeramente se necesita saber sus ventajas e inconvenientes:
Ventajas:
a) Las transmisiones por cadenas han adquirido mayor difusión para potencias de hasta 100 kW.
b) El coeficiente de rendimiento es elevado.
c) No existe resbalamiento en la rueda conducida.
Desventajas:
a) Elevado costo.
b) Son ruidosas.
c) Su vida útil H =3000 a 5000 hrs.
d) Se incrementa su desgaste en ambientes abrasivos.
Figura 4. Cadena de transmisión
1.12. Selección del Moto-reductor.
El motor puede ser elegido por catálogos, pero siempre debe cumplir que su potencia sea igual o algo mayor que la calculada en el paso anterior. En cualquier caso se obtendrán valores de N, rpm y Ka, que significan respectivamente el valor de la potencia, velocidad angular y factor de arranque.
Es recomendable preseleccionar dos o tres motores que cumplan la condición de potencia necesaria pero que tengan velocidades angulares distintas.
Figura 5. Moto-reductor.
1.13. Diseño de los árboles de las tamboras.
Se denomina árbol al elemento que tiene como función soportar y transmitir el par de torsión a los elementos giratorios de un mecanismo, por lo consiguiente los árboles resultan cargados no solo por los flectores sino también por el par de torsión que tiene lugar en toda la longitud o en algunas secciones del árbol.
1.13.1. Materiales recomendados para la fabricación de estos elementos.
Los árboles comunes, se tratan térmicamente: Ac35, Ac45, Ac40x.
Para árboles de mayor responsabilidad : Ejemplo en máquinas de elaboración, transporte, se utilizan aceros aleados que pueden ser tratados térmicamente (temple y revenido alto o temple con corrientes de alta frecuencia 40XH, 40XH2MA, 30XGT, 30XGCA.
Árboles que trabajan a muy altas rpm con cojinetes de deslizamiento.
Aceros cementables: 20X, 18XGT, 12XH3A.
Aceros nitrurables: 38X2MHOA.
1.13.2. Tipos de roturas y deterioros en árboles.
La causa fundamental de la rotura y deterioro de árboles lo constituye la (FATIGA) motivado esencialmente por:
Sobrecarga cíclica , por incorrecta valoración por parte del diseñador de magnitudes y carácter de la carga.
Valoración incorrecta de la influencia de la concentración de tensiones, condicionada por las formas de la pieza (chaflanes, chaveteros, taladros).
Concentración de tensiones condicionadas por el proceso tecnológico (huellas de maquinado, disminución de holguras indispensables).
Otra causa puede ser la falta de rigidez como resultado de flexión excesiva, se empeorarán las condiciones de trabajo de cojinetes (al variar la magnitud de la holgura, varia el espesor de la capa de lubricante).
Existen toda una serie de medidas que pueden ser tomadas como soluciones constructivas de este tipo de elemento mecánico, las cuales están dirigidas a:
Lograr igualdad de resistencia a lo largo de toda la superficie de los mismos.
Facilitar el maquinado.
Facilitar el montaje de los elementos que acoplan con ellos, así como de los árboles y ejes en sus mecanismos respectivos.
Sin embargo existen dos aspectos que por su importancia debe tratarse en lo más posible de no ser violados:
Construir el árbol escalonado de forma tal que los diámetros de las superficies de ajuste posean una dimensión no mayor a un 5% con respecto a la superficie contigua.
1.13.3. Cálculo de comprobación de la longitud de la chaveta.
La unión árbol – Cubo que será usada (unión por chaveta) ha adquirido amplia difusión debido a la sencillez y seguridad de la construcción, comodidad en el montaje y desmontaje del conjunto, bajo precio de construcción o costo entre otros factores.
Como inconvenientes de estas uniones pueden mencionarse:
Reducción de la capacidad portante de los elementos acoplados, condicionado por la disminución de sus secciones a causa de las ranuras, rebajos planos y agujeros para el alojamiento y sujeción de las chavetas, así como provocada por una considerable concentración de tensiones en estas secciones.
Dificultad de encajar exactamente (concéntricamente) las piezas.
(Drobrovolski, Zablonsky, Mak, Radchick y Erlij "Elementos de máquinas". ED. Mir. 1976.)
1.14. Cojinetes de rodamiento.
1.14.1. Clasifican los cojinetes de rodamiento.
Tabla 1.1. Clasificación de los cojinetes de rodamiento.
1.14.2. Materiales empleados para la fabricación de los cojinetes de rodamiento.
1) Anillos y cuerpos rodantes:
Acero cromado: Ejemplos
IIIX15, IIIX15CG.
Acero al cromo níquel: 12X2H4A
Los elementos fabricados con estos materiales se tratan térmicamente hasta alcanzar 60-65 HRc, con rectificado y pulido posterior.
2) Jaula: Chapas de acero. (Estampadas).
1-De bronce.
2-De aluminio. (Coladas).
3-Textolita.
1.14.3. Tipos de deterioros que pueden presentarse en los cojinetes de rodamiento.
1) Desgaste abrasivo.
2) Deformación plástica.
3) Pitting.
4) Rotura de los elementos.
1.14.4. Causas de los deterioros.
1) Imprecisiones cometidas durante el montaje.
2) Introducción durante el funcionamiento de partículas extrañas en caminos de rodadura y elementos rodantes.
3) Deficiente lubricación.
4) Introducción de agua.
5) Errores de forma y posición en el árbol y alojamiento.
6) Paso de la corriente eléctrica y presencia de vibraciones
Los rodamientos aun cuando sean eliminadas todas estas insuficiencias, al igual que cualquier otro elemento mecánico posee un tiempo de vida útil limitado.
En los rodamientos a partir de cierto período de servicio (varios millones de ciclos), aparecerán en las superficies de las pistas de rodaduras de los anillos, orificios alveolares (pitting) que aumentarán su proporción con el número de ciclos de carga, a partir de lo cual el rodamiento comienza a presentar serias deficiencias, hasta que resulta inevitable sacarlo de servicio.
Se puede asegurar que existe una relación entre la vida útil y la carga que es capaz de soportar un cojinete de rodamiento.
(Drobrovolski, Zablonsky, Mak, Radchick y Erlij. "Elementos de máquinas". ED. Mir. 1976.
Reshetov, D.N. – Machine Design. Ed. Mir. 1978.)
CAPÍTULO 2. Materiales y métodos
2.1. Metodología de cálculo del transportador de bandas.
En los siguientes subepígrafes se darán todos los papos a seguir para el diseño del transportador de banda.
2.1.1. Determinación de las dimensiones principales.
Selección de las características del material.
El material a transportar es gravilla de construcción para la cual hay que definir sus propiedades de acuerdo al análisis de laboratorio o por la tabla 2. Ver anexo No 1, Cada material tiene sus características, para nuestro material se recomienda lo siguiente:
El primer paso es establecer las propiedades del material por las:
-Tabla 1. Ver anexo No 1, determinación de la partícula representativa a´.
-Tabla 2. Ver anexo No 1, propiedades físico mecánicas de los materiales a granel.
-Tabla 3. Ver anexo No 1, codificación de los materiales a granel.
Aquí se obtiene:
Partícula representativa a´.
Peso al granel en kN/m3. El cual dividido por la gravedad en kN/h.
Ángulo de reposo estático.
Coeficiente de fricción estático entre el material y la goma.
Grado de abrasividad.
Deben además conocerse de antemano la capacidad [kN/h] y las condiciones de operación.
Hay también que establecer el ángulo de inclinación del transportador, en este caso para toda la traza, ya que el transportador es de un sólo tramo, este se define por trigonometría.
2.1.2. Comprobación de la posibilidad de transportación.
Debe cumplirse que:
(1)
Donde:
– Ángulo de fricción estático entre el material y la banda. Tabla 2. Ver anexo No 1.
– Ángulo de seguridad toma valores de 70-100
– mayor ángulo de inclinación a lo largo de la traza.
2.1.3. Selección de los rodillos superiores.
Si la capacidad volumétrica en [m3/h] < 25 ( se toman rodillos planos. Si sobrepasa este valor se recomienda emplear rodillos acanalados.
En la rama inferior se emplearan siempre rodillos planos.
La capacidad volumétrica Qv [m3/h] puede ser calculada como la capacidad Q [kN/h] multiplicada por el peso del granel [kN/m3].
(2)
2.1.4. Determinación del ancho de banda mínimo necesario.
Para rodillos acanalados o en alteza donde:
(3)
Donde:
Q– capacidad en [kN/h]
B– ancho de banda mínimo en m.
V- velocidad de transportación en [m/s]
En la tabla 17. Ver anexo No 1 se dan recomendaciones de la velocidad para distintos materiales para luego asumir un ancho de banda. Siempre que sea posible se debe escoger el ancho de banda más estrecho para la máxima velocidad recomendada, que será a su vez la velocidad más económica de funcionamiento.
C1- factor de disminución de capacidad por inclinación del transportador. Este factor aparece en la tabla 16. Ver anexo No 1
2.1.5. Comprobar la banda para los valores del tamaño representativo de partículas según las expresiones:
Para materiales clasificados. (4)
Donde:
magnitud característica del material, mm
2.1.6. Normalizar el valor del ancho de banda.
Nota: Normalizamos por la tabla 9. Ver anexo No 1.
2.1.7. Recalcular la velocidad.
Para rodillos acanalados:
(5)
2.1.8. El periodo de la banda
(6)
Donde:
L- longitud de la traza [m]
V – velocidad de transportación [m/s]
T- período de la banda [min]
2.1.9. Determinación de los pesos lineales.
a.) De la carga.
(7)
Donde:
q -peso lineal de la carga en N/m.
Q -capacidad en ton/h.
V -velocidad real calculada m/s.
b.) De la banda.
(8)
Donde:
qb – peso lineal de la banda en N/m.
B – ancho de la banda en m.
qb" – peso específico de los hilos interiores de la banda en N/m2 x mm. Tabla 6. Ver anexo No 1
Espesor recomendado para la cubierta superior Tabla 4.Ver anexo No 1.
Espesor recomendado para la cubierta inferiro Tabla 5.Ver anexo No 1.
c.) De los rodillos superiores.
(9)
Donde:
Grs – peso de una estación de rodillos en. Tabla 10. Ver anexo No 1 Para ello se necesita la clasificación del material en ligero, medio o pesado.
Lrs – distancia [m] entre dos estaciones de rodillos contiguas. Tabla 11 Ver anexo No 1
d) De los rodillos inferiores:
(10)
Donde:
Gri – peso de una estación de rodillo en la rama inferior Tabla 10. Ver anexo No 1, la distancia es el doble de los superiores.
2.1.10. Resistencia en los sectores de carga.
(11)
Donde:
qb" – peso específico de los hilos interiores de la banda en N/m2 x mm. Tabla 6. Ver anexo No 1
L – longitud del tramo.
– ángulo de inclinación de la traza.
condiciones de operación.
2.1.11. Distribución de tensiones.
Para realizar esta distribución se desarrollan los siguientes pasos:
a) Se numeran los puntos desde 1 hasta i (1 a la salida e i a la
entrada de la tambora motriz).
b) Se expresa S1 como un valor desconocido.
c) Se establece un sistema de ecuaciones que relaciona a S2 con S1 a través de las resistencias distribuidas o concentradas que existan entre ellas y se continúa así en todos los puntos hasta llegar a Si . Con este procedimiento obtendremos un total de i-1 ecuaciones.
d) Se obtiene la enésima ecuación aplicando la relación de Euler a las tensiones a la entrada y a la salida de la tabora motriz:
(12)
Donde:
Si tensión a la entrada de la tambora motriz en N.
S1 tensión a la salida de la tambora motriz en N.
Coeficiente de fricción entre la tambora y la banda.
Ángulo de contacto entre la banda y la tambora en
radianes.
El valor ese halla en la tabla 15, y se denomina coeficiente de tracción.
e) Se comparan todos los valores de tensiones en la traza con el valor de 500N y si varios de ellos son menores de 500N se tomara el menor de todos y se le asignara el valor 500N. A partir de ahí se despejaran todos los demás valores, recalculándolos en el sistema de ecuaciones establecidos en el paso (c).
f) Se comprobara el valor de tensión mínima en la rama cargada mediante la expresión:
(13)
Donde:
Smín car – tensión mínima de la rama cargada en N.
Los significados y las unidades de q; qb y lrs han sido explicados anteriormente.
Si no se cumple esta expresión se le asignará a la tensión mínima en la rama cargada el valor calculado a la derecha de la desigualdad y se recalcularán todos los demás valores de tensión despejándolos del sistema de ecuaciones establecidos anteriormente.
g) Determinación de la capacidad de tiraje
Debe cumplirse que:
(14)
Todos los parámetros de esta ecuación y sus unidades respectivas han sido definidos anteriormente.
Si esta ecuación no se cumple significa que el contacto entre la banda y la tambora no es capaz de transmitir el torque necesario. En este caso se recomienda aumentar el coeficiente de fricción (pudiera ser recubriendo la tambora con goma) o bien aumentar el ángulo de contacto mediante la colocación de tensores a la salida de la tambora motriz. En el caso de transportadores muy largos a veces es necesario colocar dos tamboras motrices y dos motores.
2.1.12. Cálculo de la fuerza necesaria en el atesador.
a) Para atesadores de tornillos:
Como estos atesadores se montan siempre acoplados a la tambora de retorno se aplicará la siguiente expresión:
(15)
Donde:
Wt – fuerza axial que debe vencer el tornillo del atesador en N.
Si y S (i+1) – son las tensiones respectivas a la entrada y a la salida de la tambora de retorno en N.
Esta ecuación se ha dividido por 2 ya que se coloca un tornillo a cada lado de la tambora.
2.1.13. Determinación del tiraje efectivo y la potencia.
a) Tiraje efectivo. Se aplica la expresión:
(16)
Donde:
Tensión en la rama de salida.
Tensión en la rama de entrada.
b) Potencia. Se determina por la expresión siguiente:
(17)
Donde:
N – potencia a seleccionar en el motor en kW.
V – velocidad de transportación en m /s
Ks – factor de sobrecarga del motor (se recomienda de 1.2-2)
– Eficiencia general de la transmisión.
2.1.14. Dimensiones de las tamboras.
Deben elegirse los diámetros adecuados de las tamboras, motrices de retorno y de desvío, si fuera necesario utilizar esta última.
(18)
Donde:
i – número de capas de la banda.
K – factor que depende del tipo de tambora y que aparece de la tabla 13.Ver anexo1.
Otras dimensiones para los distintos tipos de tambora aparecen en la tabla 14. Ver anexo1.
2.1.15. Comprobación de la resistencia de la banda.
a.) Comprobación de la banda en funcionamiento:
(19)
Donde:
i – número de capas de hilo de la banda.
K – factor de seguridad que depende del número de capas y que aparece en la tabla 7. Ver anexo 1.
B – ancho de la banda en cm.
Kt – resistencia de la banda a la tracción (hilos interiores) tabla 6. Ver anexo 1
Ku – factor de resistencia de la unión tabla 8. Ver anexo 1.
b.) Comprobación en el momento del arranque.
Esta comprobación se hace para evitar que la banda falle por el tirón que le produce el motor en el momento del arranque. Consta de los siguientes pasos:
b.1) Determinación de la fuerza dinámica.
(20)
Donde:
Sdin – fuerza dinámica sobre la banda en N.
Simp – fuerza de impulso que le imprime el motor en le arrancada en N.
(21)
Donde:
Ns – potencia de selección del motor en kW.
Km – factor que depende del tipo de acoplamiento
Tabla 2.1. Factor que depende del tipo de acoplamiento
Valor de Km | Tipo de acoplamiento | |
1.3 | Flexible | |
1.8 a 2.0 | Rígido |
b.2) Comprobación al arranque.
Debe cumplirse que:
(22)
Donde:
Smax – tensión máxima sobre la banda en N.
2.1.16. Comprobación de la tambora motriz a la presión específica de la banda.
Debe cumplirse:
(23)
Donde:
Dtm – Diámetro de la tambora motriz en m.
– Coeficiente de fricción entre la tambora y la banda tabla 15. Ver anexo No 1
Padm – Presión admisible entre la banda y la tambora. Se recomienda valores de 0.11MPa.
B – Ancho de la banda en m
– Ángulo de contacto entre la banda y la tambora en radianes.
2.1.17. Selección de la transmisión.
Consiste en determinar la relación total de transmisión con vistas a su distribución en los distintos pasos de la misma para los futuros cálculos de diseño. Esta selección se divide en los siguientes pasos:
a.) Determinación de la velocidad angular de la tambora motriz.
Se determina por la expresión:
(24)
Donde:
ntm- velocidad angular.
V- velocidad de transportación
dtm- diámetro de la tambora motriz en mm
Página siguiente ![]() |